BACK TO RESEARCH WITH IMPACT: FNR HIGHLIGHTS
As the FNR marks 25 years since its creation, we highlight 25 examples of FNR-supported research with impact. Over the past 17 years, the Plasma Process Engineering Group, headed by Patrick Choquet until his upcoming retirement, has developed solutions for anything from dental implants, protecting steel in marine environments, antibacterial surfaces as well as several types of innovative coatings.
Plasma is the result of some ingredients and a reaction on the atomic level: Plasma can be produced in the lab by heating a gas to an extremely high temperature. This causes such hard collisions between its atoms and molecules that electrons are ripped free, providing the electrons and ions needed to make plasma.
The Plasma Process Engineering Group
The Plasma Process Engineering group at LIST, headed by Patrick Choquet from its creation until his 2024 retirement, develops fundamental and technological expertise in the area of process engineering for advanced surfaces coatings. The group focuses on its recognised expertise in Research and Development of both thermal and plasma surface modification for the synthesis of functional polymer thin films, functional inorganic coatings, or functional/smart surfaces. The FNR has supported many of their research projects over the years. The team has around 10 – 15 running research projects at all times, many of them made possible by FNR funding.
Learn more about the Plasma Process Engineering Group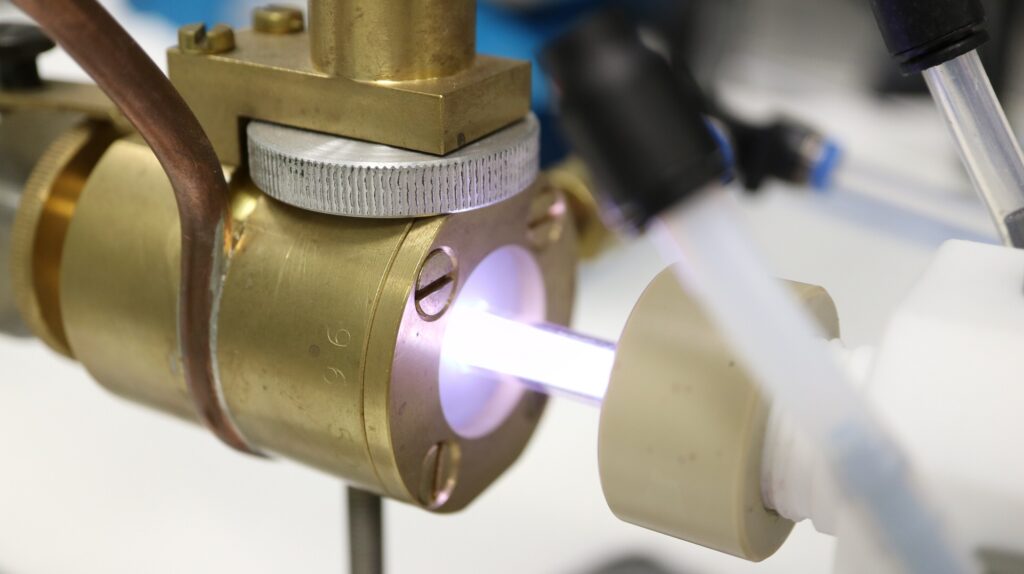
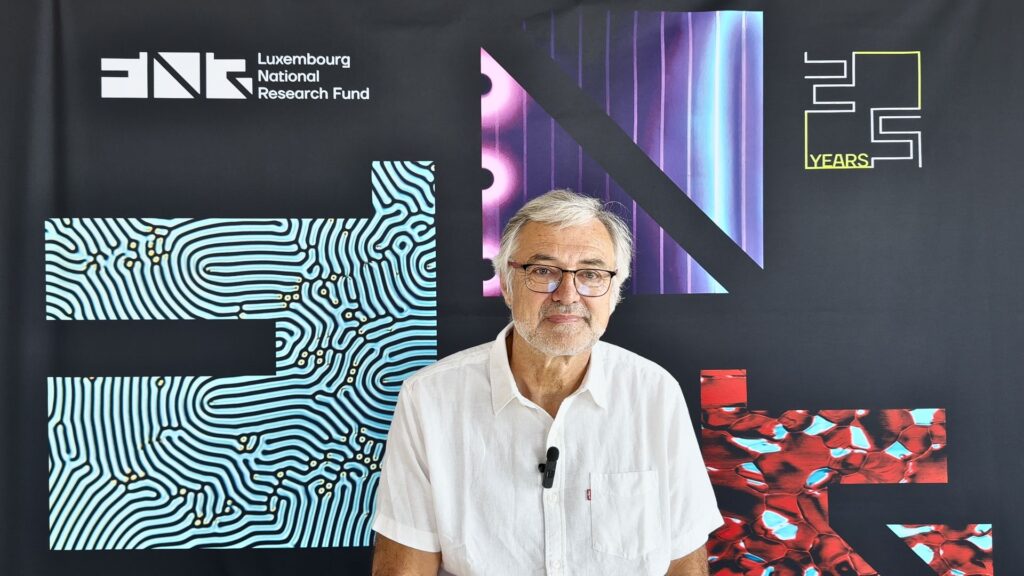
Patrick Choquet arrived in Luxembourg on August 1, 1987 to work for the Gabriel Lippmann research center, which in 2015 became the Luxembourg Institute of Science and Technology, LIST after merging with the research centre Henri Tudor. Since the creation of the FNR, Choquet has secured FNR funding for around 20 projects as main applicant, not counting the many additional projects secured by the fellow researchers in his group.
“During my time spent in these two research centers, I was able to carry out a research and technological development activity for the elaboration of new functional surfaces on different substrate materials which can be polymer, metallic or ceramic by new deposition processes using the physical and chemical properties of plasma gas,” Choquet explains.
Close collaboration with industry
It was one of the first projects where Choquet secured FNR funding in 2003 that made it possible to launch our plasma activities in the field of surface treatments in Luxembourg.
“In terms of organisation, it opened the possibility that the two Luxemburgish research institutes, at this period called, Henri Tudor and Gabriel Lippmann work together, and few years later, the two research teams merged in the LIST organisation. Thanks to this large project, we initiated collaborations with several companies in Luxembourg, such as CERATIZIT, ARCELOR MITTAL, GOOD-YEAR, CIRCUIT FOIL, and more, companies we still collaborate with today, two decades later. ”Patrick Choquet Head of Plasma Process Engineering Group at Luxembourg Institute of Science and Technology (LIST) [retired July 2024]
Collaborating with companies and international partners has been at the heart of the research group’s approach since it was created.
“If I look to the project porfolio carried out with any type of grant of the FNR, more than half helped us start collaborations with companies in Luxembourg. As a main benefit for Luxembourg, there is already our patent portfolio of the laboratory, a certain number of our patents are in co-ownership with Luxemburgish companies. With some of our partners here in the country, we have continued collaborations well after the projects supported with the FNR, such as Circuit Foil, CERATIZIT, Arcelor-Mittal, Rotarex, etc. A young company, MPG, Molecular Plasma Group based in Foetz has now built its commercial activity on plasma surface treatments that have been developed in our laboratory. This company was created in 2016 and now employs around twenty people. ”Patrick Choquet Head of Plasma Process Engineering Group at Luxembourg Institute of Science and Technology (LIST) [retired July 2024]
New coatings designed
Over the past 17 years, the researchers in the Plasma Processing Group have developed various solutions to enhance the performance of different manufacturing products. The team has, for example, tackled the issue of steel corrosion in marine environments and created eco-friendly alternatives to replace chemical methods used for bonding polymer fibers with rubber or resin with thin copper foil.
The group has also successfully designed new coatings that are both hard and resistant to high temperatures for cutting tools. Innovations also include solutions to create antibacterial surfaces, surfaces that break down pollutants using light, fire-resistant surfaces, and temperature-responsive surfaces useful for cell culture, among others.
Group members have benefitted, for example, from the FNR’s INTER Mobility programme. It enabled Nicolas Boscher to conduct a 1 year research stay at MIT in Boston. Boscher later became the first researcher at LIST to secure a prestigious grant from the European Research Council (ERC), work building on previous findings of the FNR supported project POLYMORPH.
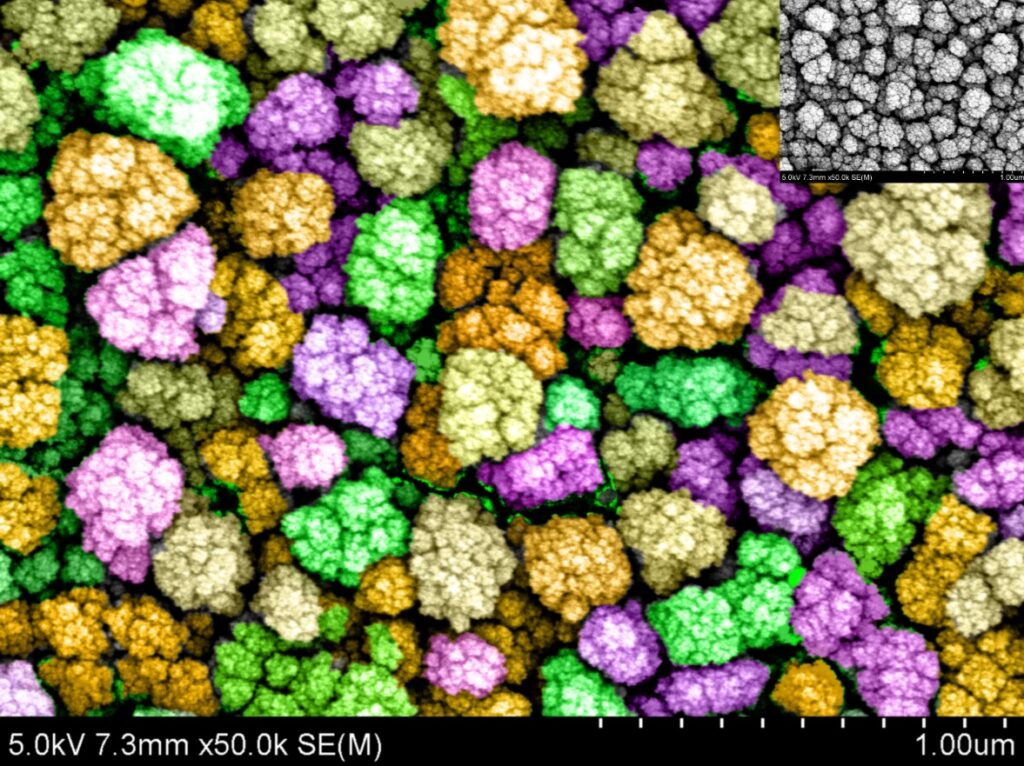
“Nano-pulsed plasma paves the way for new surface functionalities: In the field of plasma technologies, we were the first laboratory to use electrical generator able to deliver nano-pulsed plasma discharges with a very well control of its current intensities. Thank to this new technology, we have been able to synthesise new surface functionalities using atmospheric pressure plasma. We have developed so-called ‘smart polymer surfaces’ which can modify its properties when an external parameter is changed, for example, the temperature. Also, high power impulse generator was used with a physical vapor deposition technique, to improve the mechanical and oxidation resistance of nitride coatings deposited on metal or ceramic parts. ”Patrick Choquet Head of Plasma Process Engineering Group at Luxembourg Institute of Science and Technology (LIST) [retired July 2024]
Using plasma to deposit materials on surfaces
The team also used chemical molecules with macrocycles called Porphyrins to create new organic surfaces. This involves a technique called “Chemical Vapor Deposition”, where the material to be coated is placed inside a dedicated machine, some of which have been designed in Luxembourg in the Plasma and Process Engineering Group. The ions of the plasma – usually nitrogen or argon gas – then splinter the matter and deposit it on the material to be covered. It is often used for hard coatings, making them resistant to oxidation at high temperature, for example.
“The chemical vapour deposition research activity was initially supported by the FNR in the project SURFAMINE. With the help of a collaboration with the University of Mainz, in Germany, we were able to start this new area of research in the laboratory. Then, my colleague Dr Nicolas Boscher had the opportunity to prepare an ERC grant on this topic and succeeded.”
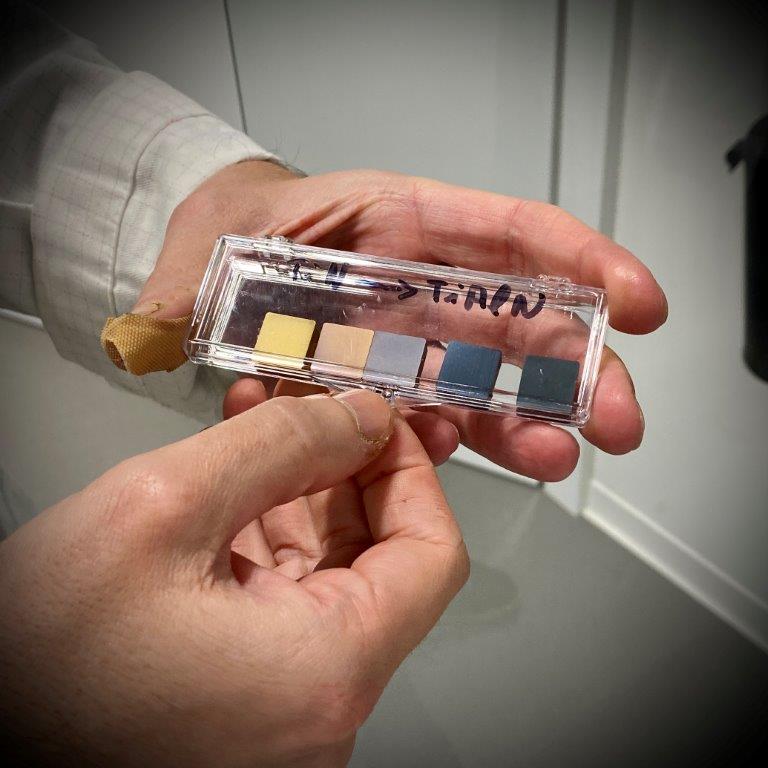
Stainless steel samples covered in different titanium-based coatings, which the researchers mainly use to put on cutting tools or drills to increase toughness and durability. Depending on the composition, the researchers get different properties with resistance to different stressors, such as friction or saltwater.
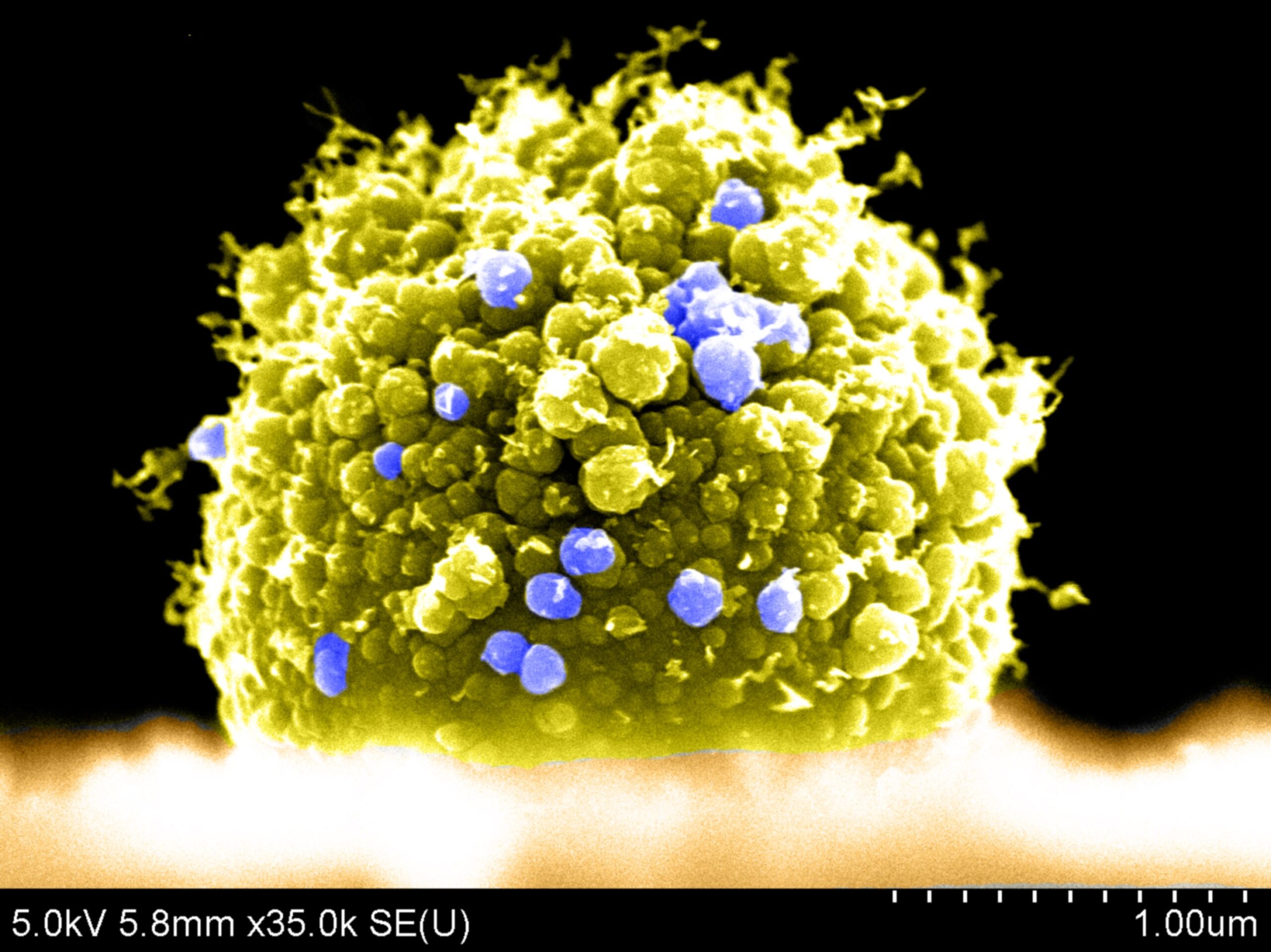
Titanium
dioxide, one of the materials deposited with the help of plasma
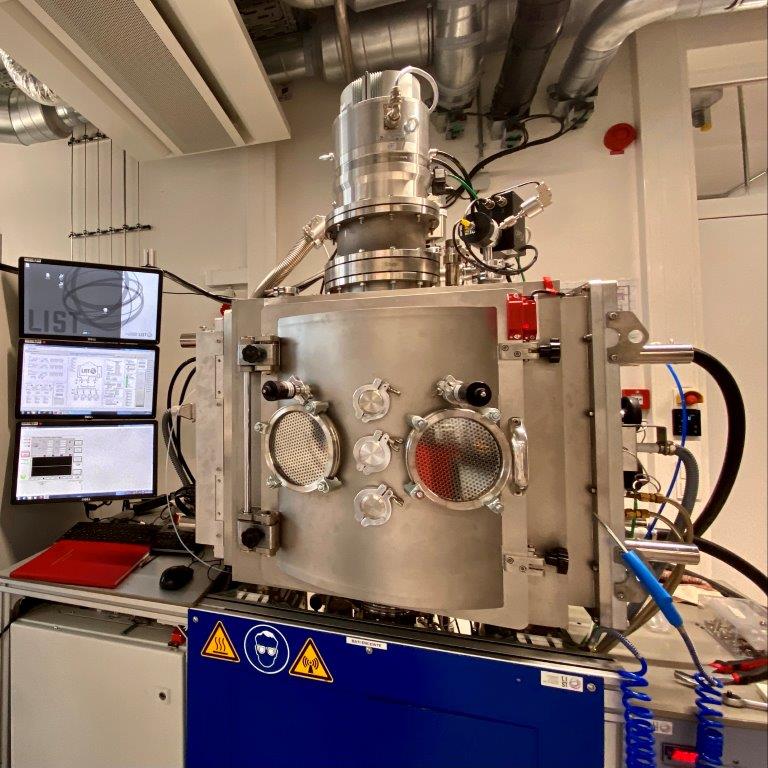
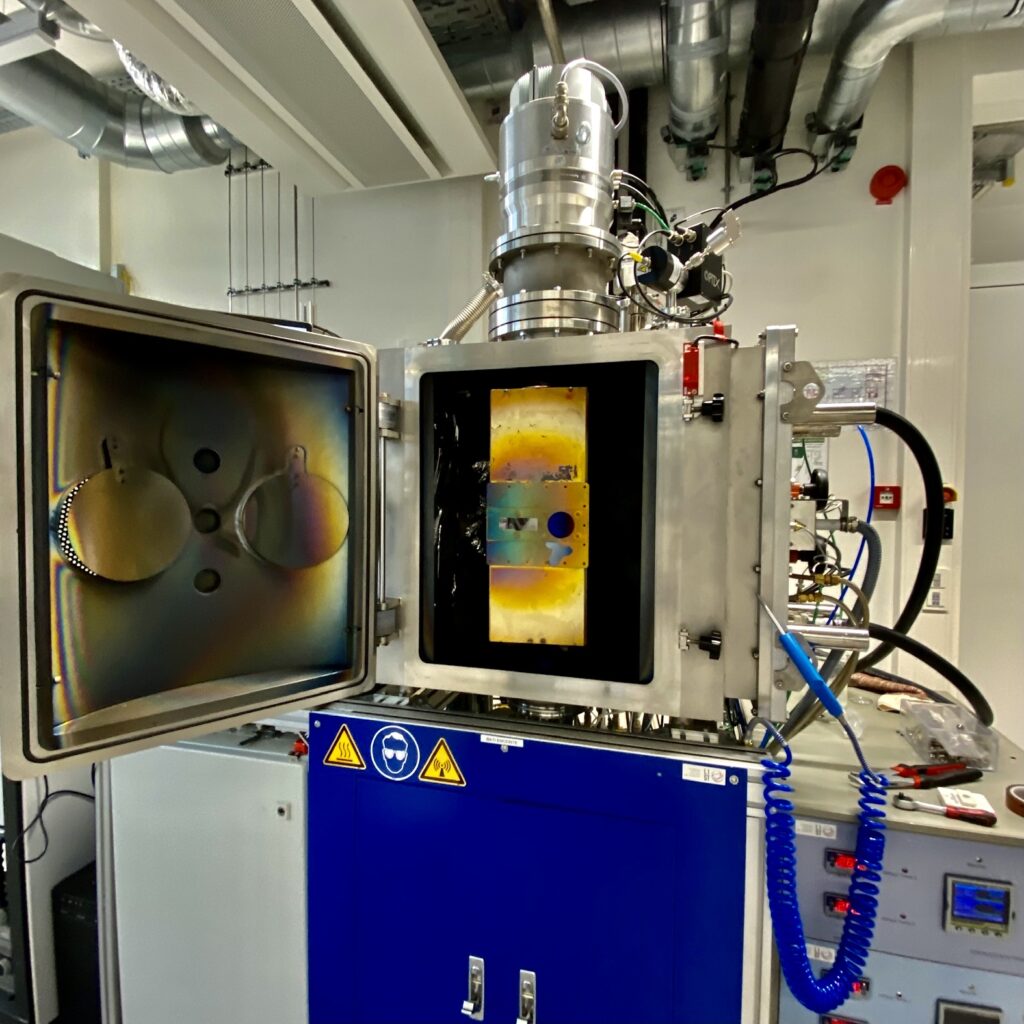
Antibacteral coating for better dental implants
The scientists in the Plasma Process Engineering Group have built, or improved, a large part of the machines in the lab.
One of them is a robot arm with a plasma torch – the Plasma Robot. It makes it possible to coat complex objects with a lot of detail – such as dental implants, screws inserted into the bone structure. The researchers are for example using the Plasma Robot to give the dental implants with an antibacterial coating, with the aim of improve the dental bone structure and avoid any rejection of the implant.
The work in dental implants is part of the BIOADBD, supported by an FNR INTER (internatioanl collaboration grant).
“During this project, we have developed a plasma surface treatment for dental implants to avoid peri-implantitis, inflammatory conditions affecting the soft and hard gum tissues around dental implants. This research was carried out in collaboration with two other public laboratories, the University of Liège and the University of Turin and small private companies in Europe in Belgium Symbiose-Biomaterials, in Italy Nobil-Bio and in Luxembourg Alkom-Digital.”
The progress of the project was taken to next level in the project BIOIMPACT, launced in 2023, supported by an FNR JUMP which supports advancing the development of applied research-driven and leading-edge technologies/concepts. This project was launched by Dr Roberto together with visiting researcher Dr Pascal De March. In 2024, the dental implant coating will be tested for in-vivo validation.
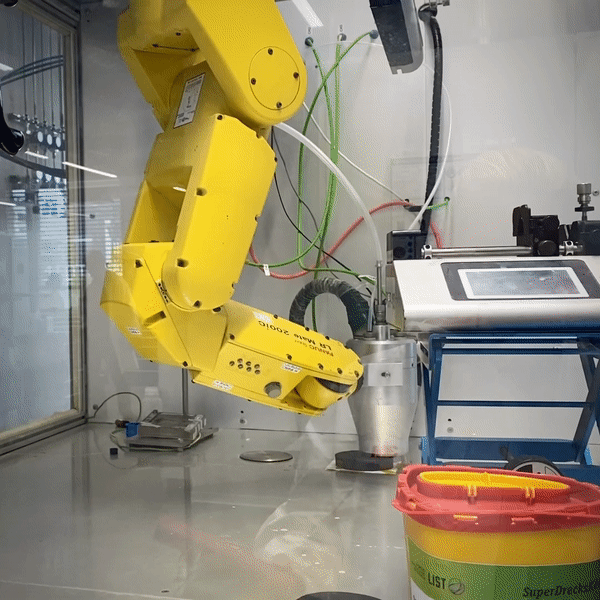
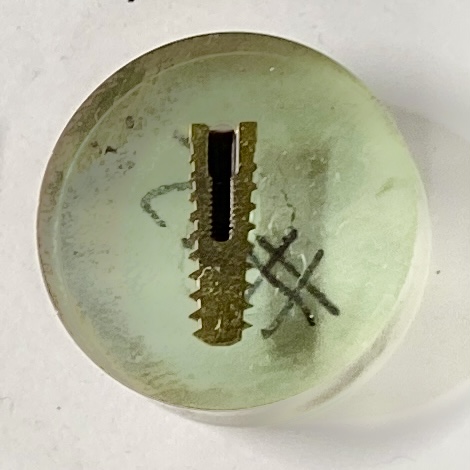
Plasma’s potential
Technologies involving plasma has a wealth of potential application areas in the future – even in cancer treatment and agriculture, and in various endeavours involving the Moon.
“In the laboratory, until now, we have mainly focused on those where plasma can be used to carry out functional surface treatments on all kinds of materials and for very different applications. But it should also be interesting to study these plasma technologies in other sectors of activity, such as health – destruction of cancer cells – decontamination of surfaces, depollution through the treatment of air, water, and also in agriculture for plant conservation. These plasma techniques can also be associated with new technologies for the elaboration of materials, such as additive manufacturing. As part of the M-ERANET project, PLACOATAM, we showed that we could combine an atmospheric plasma torch with a printer and obtain polymeric objects with much higher performance and durability. Also, plasma can be used for the spheroidization of metallic powders for additive manufacturing. We have already tested this opportunity with a laboratory in France, and the results were encouraging. We can also report that, in partnership with the ESRIC department of LIST, we have started a study on the metallurgical plasma modification of lunar materials, the regolith, for the future manufacture of objects on the moon. ”Patrick Choquet Head of Plasma Process Engineering Group at Luxembourg Institute of Science and Technology (LIST) [retired July 2024]
DISCOVER PLASMA IN AUGMENTED REALITY (AR) ON THE FNR’S LETZSCIENCE APP
letzSCIENCE is an FNR initiative to present the research the FNR supports in augmented reality (AR). From a moon rover, to cancer cells, plasma, diatoms and more, the letzSCIENCE augmented reality app features a growing collection of AR experiences, which all connect to a research area in Luxembourg.
FNR funded projects with Patrick Choquet as main applicant
Project title | Call year | Funding instrument |
Plasma Adhesive nanoFIlms on Copper foil for the manufacturing of new PCB generation | 2022 | BRIDGES |
High power Impulse Magnetron sputtering Multilayer hard nitrides coatings for “difficult-to-cut” Materials | 2020 | BRIDGES |
High Resistance Superhydrophobic Plasma films | 2019 | BRIDGES |
Low cost atmospheric pressure micro plasma coater instrument for its integration on a 2D and 3D additive manufacturing process of your proposal | 2017 | INTER |
Metal Ink Formulations for Atmospheric-Pressure and Room-Temperature Plasma-Assisted Printing of Conductive Films | 2017 | INTER Mobility |
Multilaered and nanostructured hard nitride coatings produced by high-power impulse magnetron sputtering with high temperature resistance | 2017 | BRIDGES |
Atmospheric pressure plasma TORCH for microprinting organic/inorganic functional layer | 2016 | CORE |
Plasma Assisted chemical vapor deposition of metal doped TiO2 thin film at low temperature | 2016 | INTER |
METAllic elements topcoat against corrosion in MARINE environment | 2016 | BRIDGES |
High rate deposition of functional responsive layer by an original nanosecond-pulsed plasma initiated Chemical Vapour Deposition method at atmospheric pressure (AP-PiCVD) | 2014 | CORE |
Atmospheric pressure PLASMA deposition of PLASMONIC coatings ON a WIRE substrate | 2013 | CORE |
Innovative METhod to elaborate bio-inspired stable Antibacterial surface on metallic BIOmaterials for dental implants | 2013 | INTER |
Multi-scale Computational-driven design of novel hard nanostructured Coatings | 2012 | INTER |
Elaboration of bioactive surfaces by combining Dielectric Barrier Discharge and site-spec | 2011 | INTER |
Smart sURFaces synthesized by plasma-assisted deposition at atmospheric pressure. Interaction with volatile AMINEs | 2009 | CORE |
Low temperature low cost TiO2 atmospheric pressure plasma process | 2009 | INTER |
Nanoengineering of REVersible ADhesion between a metallic and a polymer surfaces: tailoring of new functional surfaces by combination of nanotexturing and plasma polymerisation | 2008 | CORE |
Development of Innovative Surfaces by Means of Optimised Plasma Techniques and Technology Transfer to Industries | 2003 | TRASU (former FNR funding instrument) |
Related Funding Instruments
Related highlights
25 examples of research with impact: Smart materials for a sustainable future
As the FNR marks 25 years since its creation, we highlight 25 examples of FNR-supported research with impact. Since arriving…
Read more
25 examples of research with impact: Advancing AI and Computer Vision: From space tech to better healthcare
As the FNR marks 25 years since its creation, we highlight 25 examples of FNR-supported research with impact. Since arriving…
Read more
25 examples of research with impact: Understanding the evolution of the workplace in the digital era
As the FNR marks 25 years since its creation, we highlight 25 examples of FNR-supported research with impact. Active in…
Read more
25 examples of research with impact: Breaking barriers in cancer research & treatment
As the FNR marks 25 years since its creation, we highlight 25 examples of FNR-supported research with impact. In Luxembourg…
Read more
25 examples of research with impact: Shaping the future of historical research in a digital age
As the FNR marks 25 years since its creation, we highlight 25 examples of FNR-supported research with impact Andreas Fickers…
Read more
25 examples of research with impact: Harnessing nature’s power for a sustainable future
As the FNR marks 25 years since its creation, we highlight 25 examples of FNR-supported research with impact. Since arriving…
Read more